Industry & Tech Students & Alumni
Creative Control
February 7, 2019
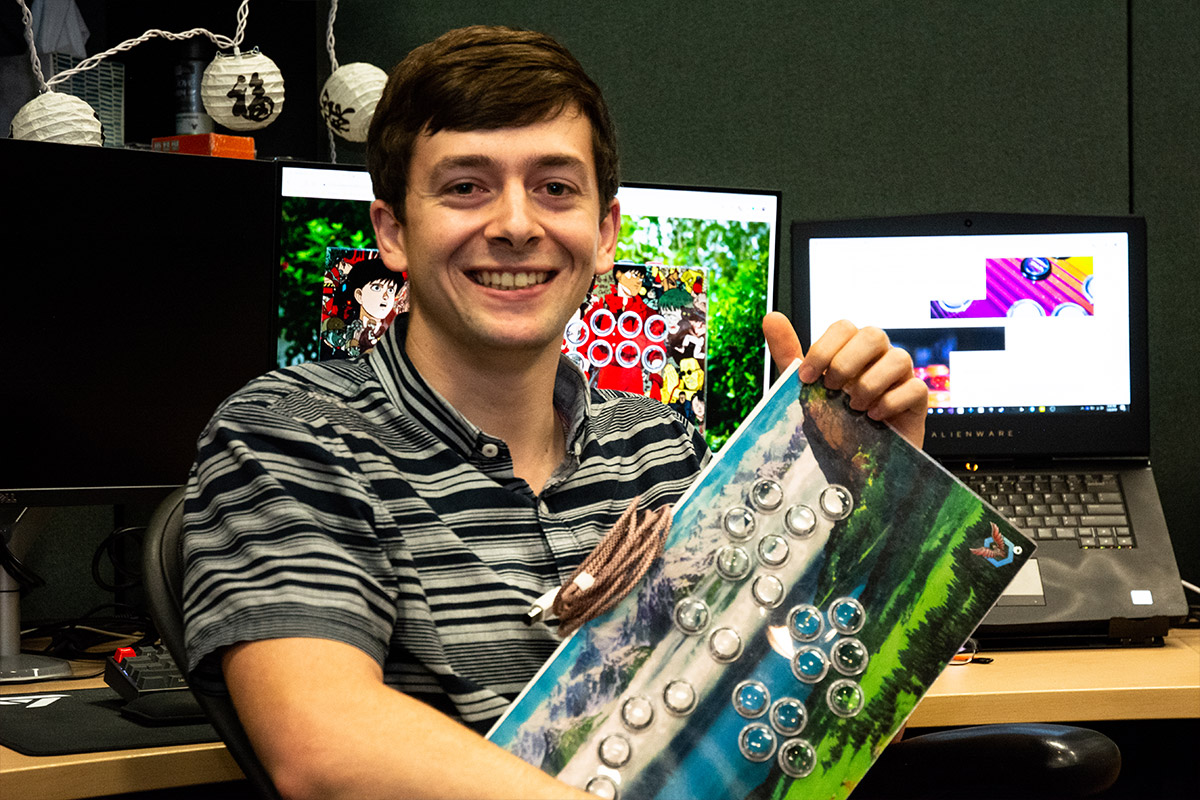
“I really like doing it. I like helping people play who couldn’t previously. And people seem to love them.”
— Aaron Cendan
Watching Aaron Cendan play a video game is like watching someone type. Instead of using a controller with joysticks, Cendan’s fingers furiously click an array of buttons on one of his own custom creations. It looks like a rectangular box with buttons that allows him to perform every move needed in a game.
“In ‘twitch’ games or really fast-moving games, a millisecond can be a long time,” Cendan says. “So having a controller that doesn’t rely on joysticks can speed up your responses.”
Cendan’s custom controllers were inspired by a friend who could no longer play games because of a hand issue. “I was surprised to find no custom controllers out there on the market, so I decided to try and build them myself,” says Cendan.
In 2018, he formed the company Stickless, and started building the boxes for competitive and disabled gamers. Now he’s got more orders than he can fill, making 85 custom controllers last year alone. This is on top of his graduate work at FIEA, where he is in the production track with a focus on audio.
Cendan says about half of his clients are disabled gamers who need a way to play their favorite games.
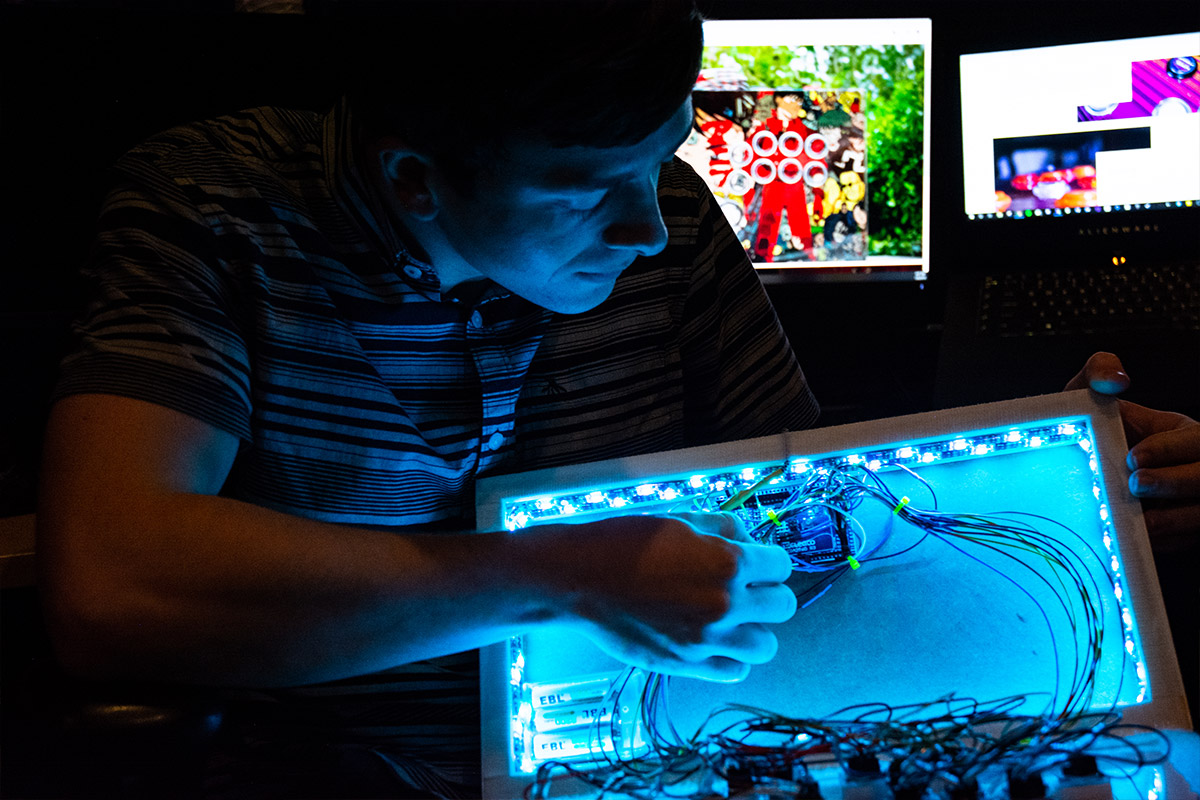
“For so long accessibility was an afterthought in the game industry, and in every industry really,” Cendan says. “And that’s no longer the case.”
The design process starts when Cendan gets clients to send a diagram of where their fingers touch the faceplate.
Then he drills the button holes using that design and builds the rest of the controller using wood, circuit boards and a polycarbonate faceplate. A contract artist working in Brazil creates custom artwork based on the client’s wishes. Each controller takes 8-12 hours to make.
“I really like doing it,” Cendan says. “I like helping people play who couldn’t previously. And people seem to love them.”